制革废水2
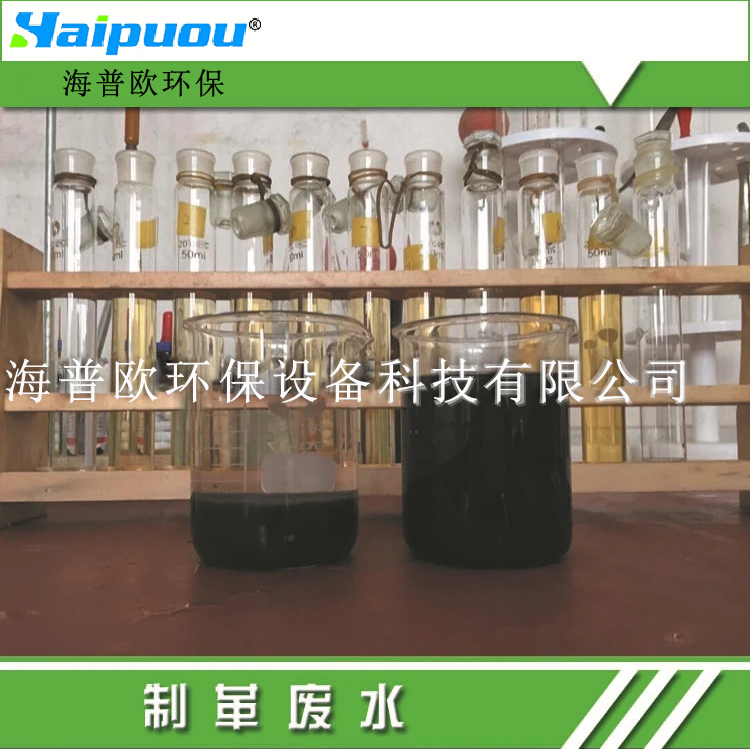
制革生产过程中排出的废水,即制革废水。通常把动物皮用盐腌或用水浸泡,使其膨润,加石灰、去肉、脱碱,然后用丹宁或铬,鞣制加脂软化,最后染色加工制成皮革。
制革废水的来源
制革生产可分为湿操作与干操作两部分。湿操作包括准备工段和鞣制工段;干操作就是整饰工段。制革废水主要来自湿操作准备工段和鞣制工段:浸水脱脂及其洗水、脱毛脱灰及其洗水、浸酸铬鞣及其洗水、染色加脂及其洗水和其他污水。制革过程中,原料皮的大部分蛋白质、油脂被废弃,进入废渣和废水中,造成废水中COD、BOD较高,成为制革废水主要有机污染源。制革废水除含有有机污染物外,通常还含有S2-、Cr3+及SS。因此,制革废水是一种高浓度有机废水,具有由染料和鞣剂造成的色度、由加入的硫化钠和蛋白质分解引起的臭味、由硫化物及三价铬引起的毒性。制革废水通常进行铬回收后再合并处理 。
制革废水的特点
制革厂废水排放量大、pH值高、色度高、污染物种类繁多、成分复杂。主要污染物有重金属铬、可溶性蛋白质、皮屑、悬浮物、丹宁、木质素、无机盐、油类、表面活性剂、染料以及树脂等。
制革废水的主要特点如下:
制革废水是高浓度有机废水,废水中COD、BOD浓度很高。
制革废水的毒性来自高浓度硫化物和三价铬,脱毛使用硫化钠,鞣制使用铬盐,废铬液中铬和硫化物的含量每升可达数千毫克,制革废水的臭味主要由蛋白质分解和添加的硫化钠造成。
制革废水中的SS高达3000 mg/L以上。
制革废水的色度主要是染料和鞣剂造成,废水的色度在600~3000倍。
制革废水总体显碱性,主要来自脱毛等工序使用的石灰、烧碱、硫酸钠,pH值常在9~10。
制革废水的氯化物和硫酸盐浓度为2000~3000 mg/L,主要来自原皮保存、浸酸、鞣制工序。
制革废水处理
制废水处理一般采用的是先分别对不同工段的废水进行预处理,再对混合后的废水进行综合处理的方法。制革废水的可生化性较好,因此生物处理是首选工艺。不过在此之前,要对含铬废水、脱脂废水、含硫废水单独收集,进行预处理。
脱脂废水通过酸处理调节PH破乳,再将破乳后的油脂经气浮法处理达到油水分离,污水排至综合废水调节池。含硫废水可采用铁盐沉降法、化学混凝法、催化氧化法等,一般多使用催化氧化进行预处理。
将以上三种废水进行预处理和其他污水一起输送至厂区污水处理厂进行生物-化学二级处理。
初级处理综合污水经细格栅、曝气沉砂池、调节池和初沉池,均衡水质水量,去除大颗粒无机物,部分COD和BOD。
生物处理,采用较多的方法有: 氧化沟、SBR法、接触氧化法,以及各种方法的组合等,要选用哪种生物处理工艺,除了考虑水质特点,还要兼顾处理水量、处理要求和场地面积等因素。皮革废水水量水质波动大,含有较高浓度的Cl-和SO42-,以及微生物难降解的有机物及铬和硫化物带来的毒性问题,因此生物处理工艺必须具备耐冲击负荷,且能适应高盐度对微生物产生的抑制作用,又能在较长时间内使难降解有机物得到降解和无机化。氧化沟的运行负荷非常低,处理效果好,且停留时间长、稀释能力强、抗冲击负荷能力强,故氧化沟是符合上述条件的首选技术。但对于中、小型皮革厂,因生产无一定规律或无足够场地,采用氧化沟工艺并非选择,而SBR工艺是间歇运行,具有理想推流的特点,且流程短;生物接触氧化法对于水量、水质的冲击负荷有很强的耐冲击能力。皮革废水相对集中排放、水质多变及负荷变化大的适合用SBR工艺和生物接触氧化法。
最后污水进入化学池进行化学混凝沉淀,凝聚剂采用碱式氯化铝,斜管沉淀。污水中SS和COD 进一步得到降低。污水处理过程中产生的初沉污泥、剩余污泥和化学污泥集中汇集,经重力浓缩、污泥调质后,进入板框压滤机压滤脱水,滤液重返污水处理系统,滤饼由当地环保部门外运集中处理。